Cobots in the Machining Transformation (MX)
The roots of manufacturing automation go back to the first industrial revolution, when water and steam power found their way into workshops.
The second industrial revolution brought the advent of electricity and mass production. In the middle of the last century, machines received their first control systems, followed shortly afterwards by the automatic changing of tools and pallets, which in turn paved the way for flexible production cells and systems. The first robots made their debut in mechanical workshops in the 1980s. And today, it is collaborative robots, among others, that are shaping the future automatically together with humans in Machining Transformation (MX).
Machining Transformation (MX) is a holistic strategy from DMG MORI that aims to make the production of the future more efficient, productive and sustainable. It is based on four pillars: process integration, in which various technologies such as turning, milling, gear cutting and other special processes and additive manufacturing are combined in one machine; automation, which includes the use of robotics and autonomous transport systems; Digital Transformation (DX), which enables the networking of machines and the use of data for optimized processes; and Green Transformation (GX), which focuses on energy savings and sustainable production.
Collaborative robots: a new era of human-machine interaction
Cobots represent a fundamental shift in the way machines and humans interact. Unlike conventional industrial robots, which usually work behind safety barriers, cobots are designed to work directly alongside and even with humans. They are flexible, easy to program and capable of performing both complex and repetitive tasks. This makes them ideal for environments that require adaptability, precision and a high degree of human-machine interaction. In industries such as CNC manufacturing, where flexibility and precision are crucial, cobots are becoming increasingly prevalent.
Cobots in CNC production: Applications and advantages
In CNC manufacturing, collaborative robots are used in a variety of applications, from workpiece handling to quality control. Cobots can load and unload CNC machines, carry out real-time inspections using integrated sensors and cameras and even support tool changes. This reduces downtime and increases production efficiency in equal measure. They can also take on complementary machining tasks such as deburring or polishing.
The integration of cobots into the processes and workflows of CNC production promises several advantages. Firstly, they increase flexibility, as they can be quickly deployed for new tasks. Cobots also increase productivity and ergonomics by taking over repetitive and physically demanding tasks. In the meantime, employees can concentrate on more demanding tasks. Cobots are also cheaper and easier to integrate than conventional industrial robots, which makes them particularly attractive for small and medium-sized manufacturers. This starts with the dialog-based programming of DMG MORI robots. It is intuitive and no special robot programming knowledge is required.
The AMR series from DMG MORI: Automation redefined
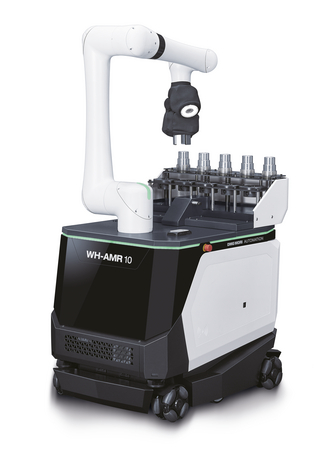
As the world's leading manufacturer of machine tools, DMG MORI has collaboratively expanded the possibilities of automation with its Autonomous Mobile Robot (AMR) series. These driverless transport vehicles can be seamlessly integrated into any CNC production environment and used for a wide variety of tasks.
For example, the WH-AMR is designed for handling workpieces weighing up to 10 kg. It can navigate autonomously through the production hall, operate several machines and improve the flexibility of work processes. For their part, the AMRs for pallet handling can carry loads of up to 5,000 kg and move freely in confined spaces - a feature that increases their added value in complex production environments. The AMR 2000 can move loads of up to 2,000 kg, making it a versatile solution for transporting workpieces, pallets or even chip containers. A version with a robot for handling tools is also available.
The AMR series from DMG MORI is equipped with advanced features that optimize both productivity and safety. These include laser sensors and intelligent image processing systems that safely protect employees from accidents. Thanks to their modular design, they can be adapted to different production layouts and integrated into existing systems.
Interestingly, the AMR series also supports the Green Transformation (GX) by optimizing internal logistics, reducing energy consumption and minimizing waste. By using these advanced systems, manufacturing companies can therefore significantly improve both the efficiency and sustainability of their processes.
Intelligent future prospects with digital twins
The future of collaborative robotics in CNC manufacturing is set to see significant progress. Artificial intelligence and machine learning will further improve the capabilities and intelligence of cobots. In the future, they will be able to adapt even better to changing workshop environments and adapt their work processes autonomously. The integration of digital twins - virtual replicas of physical machines - will also make it possible to simulate the operation of cobots before implementation, minimizing downtime and ensuring continuous improvement.
A new era for CNC manufacturing
The introduction of collaborative robots and autonomous mobile robots is a significant development for CNC manufacturing. Cobots and AMRs offer unprecedented flexibility, safety and efficiency, enabling operations to meet the rapidly changing demands of modern manufacturing environments. By integrating these technologies, companies can reduce costs, increase productivity and create more sustainable operations.
DMG MORI's Machining Transformation (MX), which focuses on Process Integration, Automation, Digital Transformation (DX) and Green Transformation (GX), is paving the way for the future of CNC manufacturing. Companies that utilize cobot and AMR technologies as part of this holistic approach will not only gain a competitive advantage, but also contribute to a more sustainable and efficient manufacturing ecosystem. As the technology evolves, the collaboration between man and machine becomes even more seamless, driving innovation and productivity to new heights.