Automated surface measurement according to standard directly in the working area
The Mahr Group from Göttingen has joined DMG MORI's DMQP program with its new contact free measurement system, MarSurf MC 510. DMG MORI Qualified Products (DMQP) are characterized by the perfect synergy of DMG MORI machines, peripherals, and accessories. The MarSurf MC 510 is a vibration-resistant, tactile free touch measurement system for measuring the surface roughness of workpieces with an accuracy of up to Rz 1.
The special feature: "With this system, users will be able to measure the surface roughness of workpieces, for the first time, according to the standards DIN ISO 4288/4287 and DIN ISO 21920-2: 2021 directly in the working area," explained Dr.-Ing. Masahiko Mori, President and CEO of DMG MORI Co. Ltd. "Furthermore, the measurement results of the MarSurf MC 510 are consistently reliable and, most importantly, can be documented in a legally compliant manner,” added Manuel Hüsken, Manuel Hüsken, CEO-Chairman of the Board, Carl Mahr Group.
In operation, the Mahr measurement system is programmatically selected from the tool magazine, positioned at the measurement location, and then precisely locked in place for the autonomous measurement process. The measurement process itself is controlled by a separate Edge PC, which communicates bidirectionally with the mechatronics of the measurement system via Bluetooth. The edge PC also interacts with the machine's CNC control via OPC UA. The MarSurf MC 510 is controlled from here via NC code, and the data obtained is also available for further analysis. By spring 2025, the system is expected to be fully integrated into the APP-based CELOS X control platform of DMG MORI.
"From a forward-looking perspective, the data obtained could even be used to draw conclusions about tool wear, which could contribute to reducing tool costs," says Manuel Hüsken, looking ahead. Additionally, this lays the foundation for future closed-loop applications regarding adaptive machining processes, as Dr. Mori adds. In this regard, there is already intensive research collaboration with universities.
Dr. Mori also sees great potential for the system in use on flexibly automated manufacturing cells and systems: "By integrating this system into the process, our customers can not only enhance the precision and consistency of their automated parts production but also significantly reduce cycle times in series production and lower overall operating costs. "
The system was showcased at the AMB in Stuttgart on the DMU 60 eVo machining center. A demonstration on the NTX 500 turn & mill center will follow in November at JIMTOF. DMG MORI will also present the MarSurf MC 510 in action at the showrooms in the production facilities in Iga, Pfronten, and Seebach.
Highlights: MarSurf MC 510
- Automated surface measurement according to standards DIN ISO 4288/4287 and DIN ISO 21920-2: 2021
- Automated in-process measurement of surface parameters in the working area
- Reproducible results with maximum precision
- Standards-compliant and legally secure documentation of surface parameters
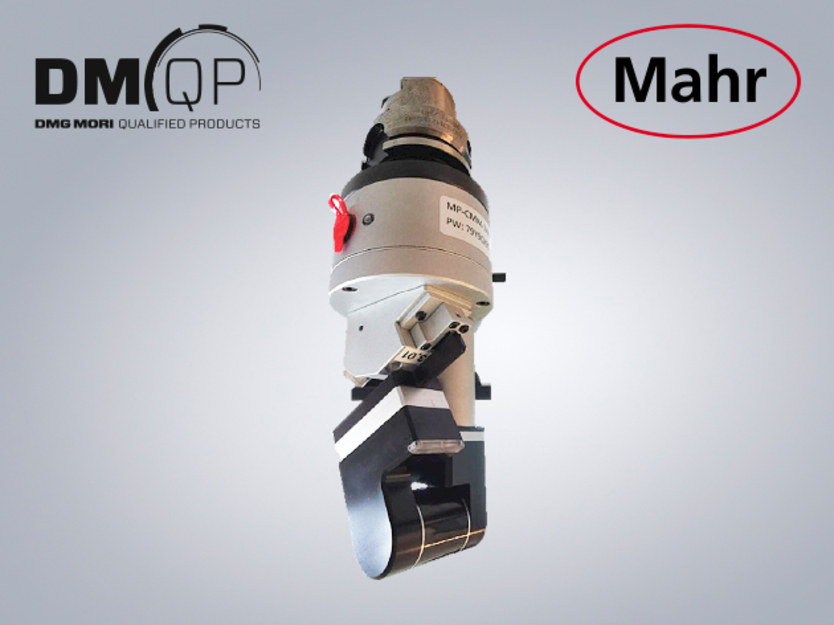