Capacity increase by means of robot automation
WILHELM BAHMÜLLER Maschinenbau Präzisionswerkzeuge GmbH from Plüderhausen has its roots in a mechanical workshop that was established in 1945.
Starting with circular shears, the company soon laid the foundation for its corrugated cardboard processing business, which is still successful today. Over the years, the range of services has been extended to include precision grinding, automation and precision tools. 400 experienced engineers now ensure that the company’s processes run smoothly, from development to production and on to sales and service. BAHMÜLLER has been manufacturing using machine tools from DMG MORI for more than 40 years and currently uses ten different models. Since 2023, the company’s investments in modern manufacturing systems have included automation solutions. For example, a CTX 1250 beta TC was retro-fitted with a Robo2Go in 2023. A CLX 450 TC followed later in the year, which was also equipped with user-friendly robot automation. This has put BAHMÜLLER in a position to reduce its production costs and counteract a shortage of skilled personnel.
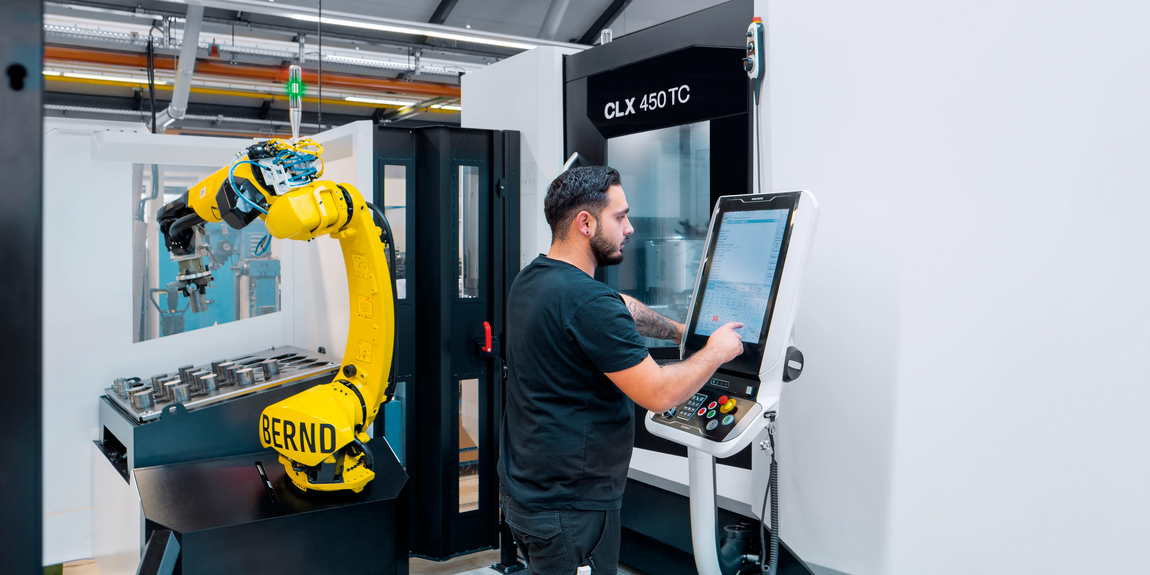
Design and development of precision tools
Its high quality and reliability standards have made BAHMÜLLER a competent partner in the manufacture of precision tools. “We fulfill all requirements for machining with our standard range of products for all of the most popular spindle connections, and also customizations,” explains Hans Binder, the head of the precision tools business area. “We support our customers with an innovation-oriented team, right from the design and development stage.” BAHMÜLLER safeguards the future of this team by providing plenty of training and currently has 37 apprentices.
BAHMÜLLER combines technical expertise with modern manufacturing solutions. Older machines are regularly replaced with technologies that are more innovative. 5-axis simultaneous milling centers such as the DMU 125 P duoBLOCK and DMU 160 P duoBLOCK have already been in use for many years, and turning-milling centers are also becoming increasingly important. “We have been able to drastically reduce our throughput times and increase our capacity by integrating different manufacturing technologies in a single workspace, even to the extent of complete machining in an ideal case,” says Hans Binder, looking back at this development. Complete machining is also regarded as an efficient way of fulfilling the increasing demands that are being made with regard to precision.
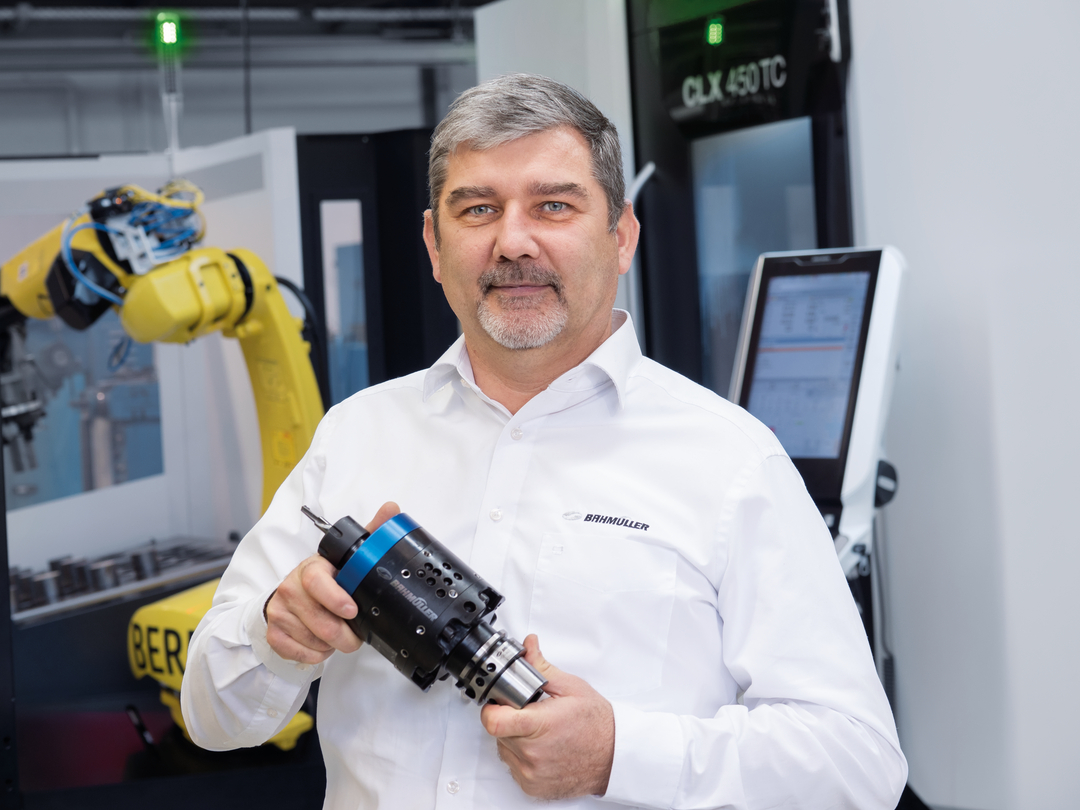
6-sided turn-mill complete machining
After installing two CTX beta 1250 TC turning centres, a CLX 450 TC was purchased in 2023. “The work area is of a similar size and in this case we did not need 5-axis simultaneous milling,” says Hans Binder, justifying the purchase of the entry-level model for turning and milling. “The attractive price obviously made the decision easier. The machining of workpieces, including tool bodies and milling heads, takes place from all 6 sides in a single process. “The finished products only require burnishing and grinding.”
BAHMÜLLER took a new step towards extending capacity in 2023 with the initial automation solutions. Hans Binder sees DMG MORI as the right partner for this: “The extensive range of automation provides a sufficient amount of choice to get started in this area.” Robo2Go is regarded as the perfect example. “DMG MORI succeeded in retrofitting the robot on the CTX beta 1250 TC very easily and the CLX 450 TC was installed as a complete, automated system.” In both cases, it only took a day to train an operator to use the app-based control of the Robo2Go. “The system is self-explanatory and intuitive, because it guides the user through the process.”
Low production costs thanks to unattended shifts
In practice, both Robo2Go systems integrate into the everyday working environment in an optimum way. “We produce individual parts and small batch sizes with short run times on the CLX 450 TC during the day at the same time as working on other machines,” says Hans Binder, describing the process. An additional employee is not required. “At night and over the weekend, we process bigger batches of up to 30 parts and components having longer running times completely unattended.” In this way, BAHMÜLLER has increased its capacity significantly and reduced production costs at the same time. The range of components varies between ø 20 mm and ø 175 mm, which is the maximum diameter of the gripper. The load capacity of the Robo2Go including the gripper is 35 kg, which is more than enough for the relevant workpieces.
Safely into the future thanks to automation
BAHMÜLLER has successfully achieved entry into automated production with the two Robo2Go machines. In the light of anticipated challenges, Hans Binder is looking ahead with confidence. Automated production will be an important topic in future investments: “Both the shortage of skilled staff and the geopolitical situation will continue to be concerns in the coming years. Against this backdrop, automation solutions will be indispensable in order to remain competitive.”
WILHELM BAHMÜLLER Maschinenbau Präzisionswerkzeuge GmbH
Wilhelm-Bahmüller-Straße 34
73655 Plüderhausen
Germany
www.bahmueller.de