Digital Twins in Connected Data Architectures
Digital twins are considered a key technology in Digital Transformation (DX). They enable the precise virtual representation and simulation of machines, tools, and manufacturing processes. This allows complex machining tasks to be optimized in advance and entire manufacturing solutions to be planned efficiently. However, to reliably fulfill their tasks, digital twins require various types of data depending on the application, such as:
- Workpiece-relevant parameters
- Sensor measurements
- Maintenance data
- Production data
The challenge lies in capturing, managing, and making these heterogeneous data available to digital twins in an open, interoperable, and connected manner.
Interoperable Standards for Connected Data Architectures
A crucial foundation for the necessary data architectures is open standards and interfaces. These make it possible to share data across different systems and applications without proprietary dependencies, significantly facilitating integration and collaboration between different stakeholders. Key elements of an open data architecture include:
- Open protocols such as OPC UA
- Standardized file formats (JSON, XML, RDF)
- IoT platforms and cloud technologies for data collection and processing
Asset Administration Shell as a Key Technology
A key role in linking open data architectures is played by the so-called Asset Administration Shell (AAS). This "administration shell" represents a digital twin of all involved assets—whether machines, components, products, or services. Specifically, the AAS describes all relevant information and functions of an asset, forming the basis for implementing digital twins.
While the digital twin provides a dynamic, constantly updated representation of an asset, the AAS delivers its structural and functional foundation. It includes both static information, such as technical specifications, and dynamic data, such as current sensor measurements. In CNC manufacturing, an AAS could represent an entire machine tool, containing:
- Machine master data
- Current operating parameters
- Simulation data for wear prediction
- Standardized interfaces (e.g., OPC UA, REST API)
The AAS then enables seamless integration of the machine tool with other systems—such as an ERP system for production planning or a cloud platform for AI-driven analysis.
Factory-X: A Platform for Connected Manufacturing
A current example of the implementation of connected open data architectures is the Factory-X project. As the largest funded initiative within the German (and increasingly international) Manufacturing-X initiative, it brings together leading players from the machinery and IT industries, including DMG MORI.
The core element of Factory-X is the development of a standardized software architecture for the manufacturing industry. The "Factory-X Kernel" aims to simplify the integration of IT and OT (Operational Technology) systems, laying the foundation for fully connected production.
The Future of Connected CNC Manufacturing
The development of connected open data architectures will fundamentally change CNC manufacturing. Some promising future perspectives include:
- Self-optimizing production systems: AI algorithms will increasingly be able to learn from collected data and autonomously optimize manufacturing processes.
- Cloud-based technology databases: Central platforms could provide proven machining strategies and optimal parameters for various machining tasks.
- Augmented reality in manufacturing: AR technologies accessing connected data could assist operators in machine setup and quality control.
- Collaborative production networks: Standardized data exchange will make it easier to flexibly share manufacturing capacities among partners, balancing workload fluctuations.
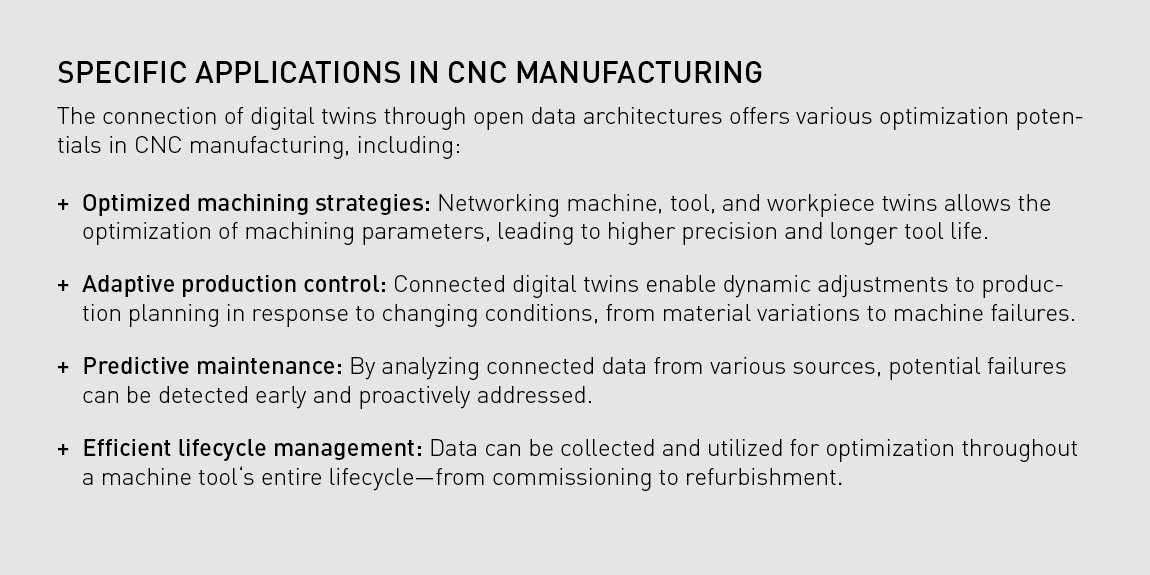
Conclusion
Connecting digital twins through open data architectures holds enormous potential for CNC manufacturing. It enables unprecedented transparency, flexibility, and efficiency in production. At the same time, it challenges companies to further develop existing systems and processes. The key to success lies in the consistent use of open standards and close collaboration among all stakeholders.